11月19日,深中通道项目钢箱梁制造启动大会在中铁工业旗下中铁山桥南方工程装备公司举行。深中通道管理中心副主任范传斌,桥梁工程管理部部长姚志安,中山翠亨投资有限公司总经理刘嵘,深中通道项目JL06标总监理工程师龚红星等领导出席仪式。启动大会上,深中通道管理中心副主任范传斌宣布深中通道钢箱梁制造G05标项目正式启动。他强调要严格执行各项制造程序和质量标准,高起点、高质量、高标准地抓好钢箱梁制造的各项工作,谱写深中通道建设的新华章。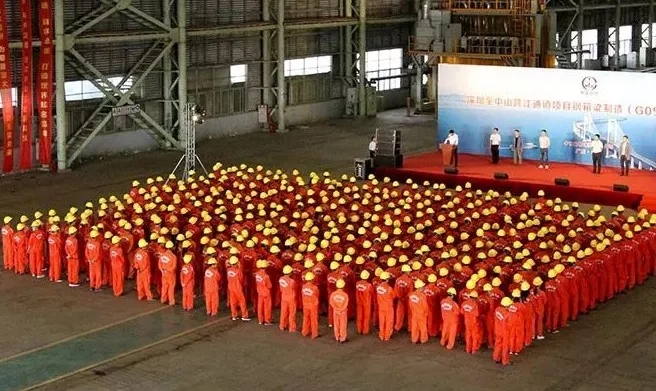
深中通道是继举世瞩目的港珠澳大桥后的又一世界级桥梁工程。在10月29日,中铁工业所属中铁山桥和中铁宝桥分别与广东省公路建设有限公司正式签订深中通道项目G05、G04两个标段、共约 18.4 万吨钢箱梁制造合同。
下面,让我们了解一下世界级超大集群工程——深中通道项目钢箱梁制造“智能制造”解决方案。
深中通道的建设将是继港珠澳大桥后我国交通基础设施建设领域的又一个重要的里程碑,目前,是我国乃至世界上技术难度最大、建造工艺最复杂的工程之一。
| 集“桥、岛、隧、水下互通”于一体的世界级跨海通道工程,项目总长约24公里,钢箱梁制造是深中通道主体桥梁工程的重要组成部分。 |
| 设计使用寿命100年,须满足安全、优质,智慧、高效,耐久、经济,环保、美观的要求。 |
| 推动大湾新区从“走廊”发展向“环湾”发展转变,对粤港澳融合发展,建设国际一流大湾区和世界级城市群将产生积极影响。 |
| 大桥预计于2021年开始架设,2023年完成相应制造,全线计划于2024年建成通车,对钢箱梁的加工制造质量和工期控制提出了很大的挑战。 |
以“建设世界一流桥梁”为目标,坚持创新驱动,以设备、工法、工艺为核心,提升工程质量,保障工程耐久性,推动钢箱梁制造模式变革,努力把该项目打造成新时代“交通强国”钢桥梁制造的新标杆,通过深中通道项目,产生广泛而长期的示范性影响,传播“中铁工业、世界品牌”企业愿景。
深中通道世界最大跨径海中钢箱梁悬索桥——伶仃洋大桥效果图
中铁工业时刻关注行业技术进步,经过多年积淀和技术提升,形成了先进的造桥理念,特别是在正交异性钢桥面板领域,参与了港珠澳大桥、虎门二桥、青山长江大桥等多个项目的国家级课题的研究,对正交异性板的疲劳有深刻的认识。为此,在深中通道钢箱梁制造中推行钢结构智能制造,以“两化融合”(工业化、信息化)为基础,推进“互联网+桥梁制造”建设,以解决正交异性桥面板疲劳损伤等钢箱梁通病为突破点,充分借鉴沉管隧道钢壳智能制造项目的实施经验,实现工业无线网络全覆盖,建设基于BIM技术的项目管理协同制造云平台,对现有的关键工序进行设备升级,对制造技术进行改进和提升,吸收机器人、BIM技术、数字技术、信息化技术的新成果,推行制造生产线中BIM技术、智能装备的实施应用,通过智能化管控,高标准、高质量、高效率完成好这项伟大的世纪工程。
充分发挥中铁山桥南方工程装备公司、中铁宝桥(扬州)公司,两个生产基地优势,强化项目综合集成管理,以质量管理和生产进度管理为核心载体,集成物资管理、技术管理、运输管理、风险管理等各项要素,全面规划、统筹协调、集成资源、综合控制,有序高效地推进钢桥梁制造。
构建以板材智能下料切割生产线、板单元智能焊接生产线、节段智能总拼生产线、钢箱梁智能涂装生产线以及车间制造执行智能管控系统为核心的“四线一系统”,推进我国桥梁制造向信息化、智能化发展,全面促进钢箱梁制造产业的转型升级。
利用传感网络化综合集成技术,深中通道钢箱梁智能制造将自动化生产线、焊接、装配、涂装机器人等数字化制造装备有机地集成在一起,通过执行指令、工作状态和运行管理等制造活动之间信息的实时交互,夯实钢箱梁智能制造的核心能力的技术基础,推动桥梁制造模式的深刻变革,创新中国桥梁建造发展模式。
| 已形成了完整的、可实施的、稳定可靠的U肋双面全熔透焊接技术,达到U肋焊缝全熔透、无缺陷、可检测要求。 |
| 在行业内率先完成了组焊一体技术的开发和设备的安装调试,质量稳定可靠,为本项目的实施奠定了基础。 |
| 拥有完整的三维测量设备及数字拼装技术,成功应用于北京永定河大桥、虎门二桥等多个项目。 |
| 完成连续焊接、热包头焊接试验,消除该部位焊接初始缺陷。 |
| 创新性提出基于电磁的无损支撑系统,实现总拼快速、无损伤组焊,已完成试验。 |
我们比历史上任何时期
都更接近中华民族伟大复兴的目标
不久的将来
一个世界级超大集群工程
在我们这一代人手中实现
大潮起珠江
站在历史和时代发展的潮头
唯有锐意进取
敢为人先
才能书写时代华章
中铁工业欢迎您